Introduction
The quality of food defines the standard of health and well being. The quality of food diminishes due to several distinct components; one such is the modern food packaging system. It is a vexatious topic to deal with. There is a worldwide explosion in the consumption of hot beverages like coffee, tea, and hot chocolate. They have been a part of our daily lives; various factors influence them, and the consumption pattern varies among individuals. The consumption of these beverages was not a debate here; the actual concern is with the single-use cups. These beverages were largely consumed in metal, glass, plastic, paper cups, paper board cups, and even in silicon and Styrofoam. Out of them, the plastic cups were used earlier. The devastating effects of plastics on humans and the environment need an alternative solution. This, in turn, filled the spot with paper-based cups. Presently, paper cups and cardboard cups are used on a massive scale in food supply chains serving beverages. The market for paper cups is projected to grow from USD 10.61 billion in 2022 to USD 13.55 billion by 2030 [
1]. Paper naturally weakens and tears when it comes into contact with water. It results from the cellulose in paper being broken down by chemical processes. Therefore, to counteract it, the inside surface of the paper-based cups is coated with a thin layer of plastic. By acting as a barrier, this layer stops the water and paper from reacting. It also gives the cups a strong foundation. Coating a plastic layer sounds like a clever idea; on the superficial view it is a paper-based cup, a greener alternative, but in an integral view, it is a disguised plastic cup, which serves no use and is only a burden to both humans and the environment. The plastic layer limits the recyclability of the paper-based cups. On exposure to higher temperatures, the hazardous components that migrate from the plastic layer into the beverages are the major concern. At high temperatures, it has been shown that the plastic liners used in paper coffee cups can produce harmful ions including fluoride, chloride, sulfate, and nitrate, as well as compounds like bisphenol A, phthalates, and tetrabromobisphenol A [
2]. The health impacts include carcinogenicity, obesity, early puberty, reproductive toxicity, and hormone disturbances [
3]. When exposed to heat, the materials used to produce the paper cups also have a tendency to move apart from the plastic layer. The paper cups were made using paper board, additives, adhesives, inks, plastic coating, and bleaching agents.
Adhesives and printing inks release phthalates and alkylbenzenes into the drinks. The amount of chemical additives that migrate into food might vary depending on temperature, storage duration, food type, and other variables. These chemicals include enzymes, emulsifiers, and preservatives, which are utilized in the making of paper cups [
4]. The micro plastic coating on the cup breaks down and releases about 25,000 micron-sized micro plastic particles into the hot liquid within the paper cups in fifteen minutes [
5].Micro plastics are dispersed, and the plastic coating is broken down at temperatures over 80 °C. Bleaching chemicals included in paper cups, such as hydrogen peroxide, sodium hydrosulphite, and sodium dithionite, can move into food at high temperatures. Paper and cardboard are formulated with per- and polyfluorinated alkyl compounds to give the package protection against moisture, oil, and other lipids [
6].
Exposure to these chemicals has been linked to many health risks, including elevated cholesterol, altered liver enzymes, decreased antibody response to certain immunizations, preeclampsia and pregnancy-induced hypertension, slight birth weight reductions, and kidney and testicular cancer [
7]. Numerous endocrine issues, including early puberty, hormone-dependent tumors like prostate and breast cancer, and a range of metabolic illnesses, including polycystic ovary syndrome, have been connected to bisphenol A [
8]. BPA can increase the risk of mammary tumorigenesis [
9] and hepatic tumors [
10]. It is an obesogenic that interferes with insulin production and impacts lipid metabolism, glucose metabolism, and adipose tissue [
11]. Phthalates cause intrauterine growth limitation, reduce placental weight, interfere with ovarian activities, and impede cell proliferation [
12]. Additionally, it causes testicular and hepatic tumors [
13].
Is using paper cups a better option in light of these health effects? But there is no alternative to opt for; however, there is definitely an idea to fix this issue of the leaching of chemical components into beverages. Creating a barrier layer above the plastic coating can be a game-changer. The barrier layer needs to be inert, biodegradable, tamper-proof, temperature and water resistant. One such material that holds all the desirable properties and can be effectively used as a barrier layer is dried areca leaf sheath. The current study outlines the application of dried areca leaf sheath to paper based cups, which prevents the leaching of chemicals into the food products.
Areca leaf sheath
The areca leaf sheath is an agro-waste from the areca palm tree. Areca catechu is the scientific name of the areca palm. It is widely grown in the tropical Pacific, Asia, and parts of east Africa [
14]. The leaves have a high tensile strength, are rigid, impermeable, and biodegrade slowly [
15]. Currently, these leaf sheaths are used for the production of disposable plates, cups, tubs, trays, and cutlery sets.
By 2032, the palm leaf plate market is expected to have grown from USD 436.3 million in 2023 to USD 706.41 million [
16]. Additionally, areca leaves were pulped, combined with other pulps, and used to make packing paper boards [
17]. Alkaloids, including arecoline and arecaidine, fat, gum, tannins, gallic acid, and catechin, are all present in the leaves [
18]. Areca exhibits a number of therapeutic qualities, including analgesic, hepatoprotective, antifungal, antibacterial, anti-inflammatory, antidepressant, antifertility, hypoglycemic, antiulcerogenic, wound healing, and abortifacient effects [
19,
20,
21,
22,
23]. It also demonstrates hypoglycemic effects, antihelminthic activity, mitotic activity, and cholinomimetic activity.
With a tensile strength of 163.36 MPa along the grain direction and 0.18 MPa along the transverse grain direction, the leaves' sheath was made of strong natural material [
24]. Nevertheless, the tensile strength decreases as the leaves are shaped. Areca nut leaf sheath fiber is mostly made up of lignin, α-cellulose, and hemicelluloses. Furthermore, it includes trace amounts of pectin, fats, and waxy substances. The sheath of leaves typically ranges in thickness from 1.5 to 4 mm, with a moisture content of 55% when wet and 11% when dry [
25].
Drawbacks of Areca sheath cups: These cups tend to break easily, are brittle, have less structural integrity, are less durable (can’t withhold hot or cold beverages for prolonged periods of time, might leak), have seasonal variability, are heterogeneous in material color, texture, and thickness, have poor heat insulation, and can accumulate dust and dirt if not properly stored.
Ideation: Considering the fallbacks of the areca sheath-based cups, they cannot be widely used, like the polyethylene-coated paper cups, despite being organic and plastic-free. But the areca cups can still be employed along with the paper cups coated with a plastic layer. The paper cups and areca sheath cups were to be manufactured separately, and then the areca cups were inserted into the paper cups to make the areca sheath-paper cups, preventing the migration of chemical components from the paper cup into the food products. Here, areca sheath was utilized as a barrier layer.
Method of manufacturing of Areca sheath-Paper cups (ASP Cups):
Materials required: Paper board, adhesives, inks, PE coating, and areca leaves sheath.
The plastic cups were made following the general method.
Preparation: Acquire food-grade paperboard.
Printing: Desired designs were printed on the paperboard.
Cutting: Die-cut the paperboard into cup blanks and bottoms.
Shaping: Form the cylindrical shape, seal the side seam, and attach the bottom.
Coating: A thin layer of PE was coated inside the cups.
Curling: Roll the top edge to form a rim.
Areca cups were manufactured by following the steps provided.
Cleaning: Distilled water was used to clean the sheaths of areca leaves that were gathered.
Drying: For eight to twelve hours, the leaves were exposed to sunlight.
Hydraulic press molding: Dried leaves were pressed and stamped for 40–60 seconds in a hydraulic press mold machine with the top and lower die temperatures set to 110–115 ˚C and 35–45 ˚C, respectively [
26].
By following the measurements specified in
Table 1, we can achieve a tight fit while ensuring that the Areca cup can be easily inserted into the paper cup.
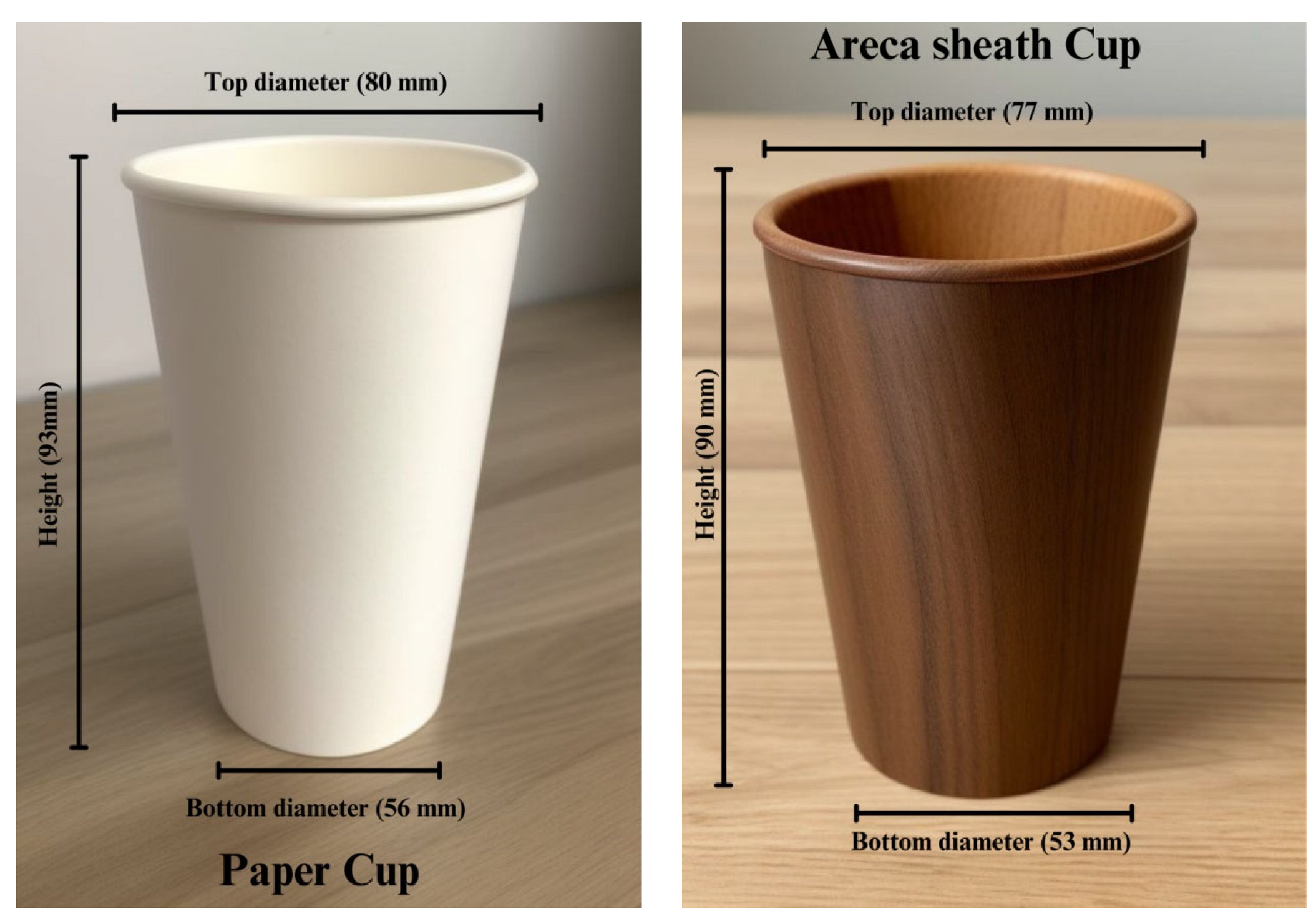
The final process includes stacking the areca cup inside the paper cup secured by food-grade adhesive, which forms the Areca sheath paper (ASP) cup.